伊藤製作所の技術開発におけるポリシー
- 開発者、設計者、メーカーの課題
- 伊藤製作所の課題解決力(つよみ)
- 研究開発力
- 技術力
- 設備力
- 品質力
- 人財力
- CHALLENGE精神
- トライ&エラー
- 技術開発・技術力の向上
- 新しい価値を生み出す製品へ
技術開発事例
R&D CASES
- せん断技術
- 曲げ技術
- 絞り技術
- 板鍛造
- システム開発事例
せん断技術
1992年
今日ほど優れた型材や潤滑油、コーティングが存在しなかった30年前から精密せん断技術で歯先のダレを極力抑えたディテントの量産に成功。
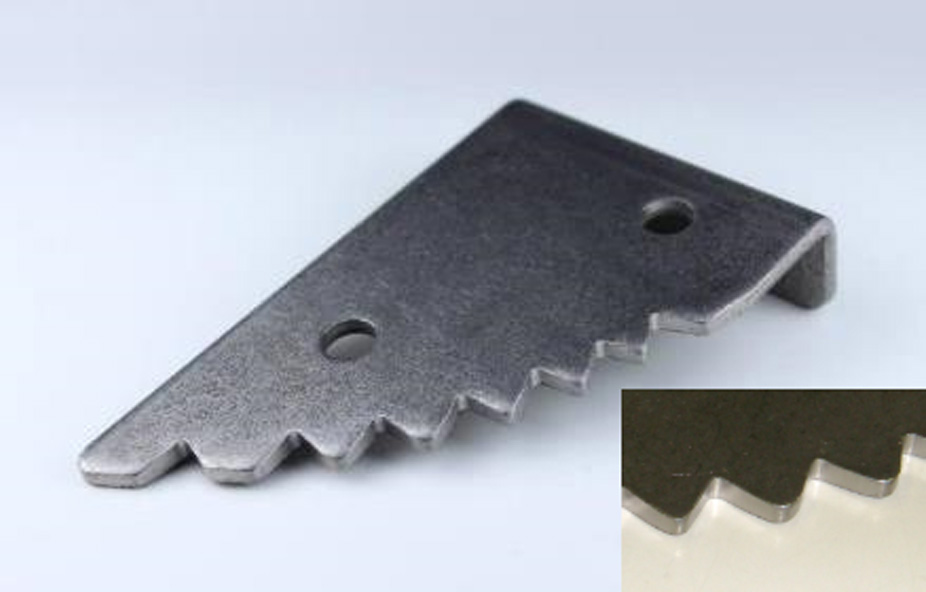
設備 | 200トンクランクプレス |
---|---|
品名 | ディテントプレート |
材質 | SPHC |
板厚 | 3.2mm |
2000年
折りたたみ式携帯電話のヒンジ部品。板厚2mmに対し、せん断面長さ1.5mmを維持しながら巾0.45mmの側壁成形順送りプレス化。
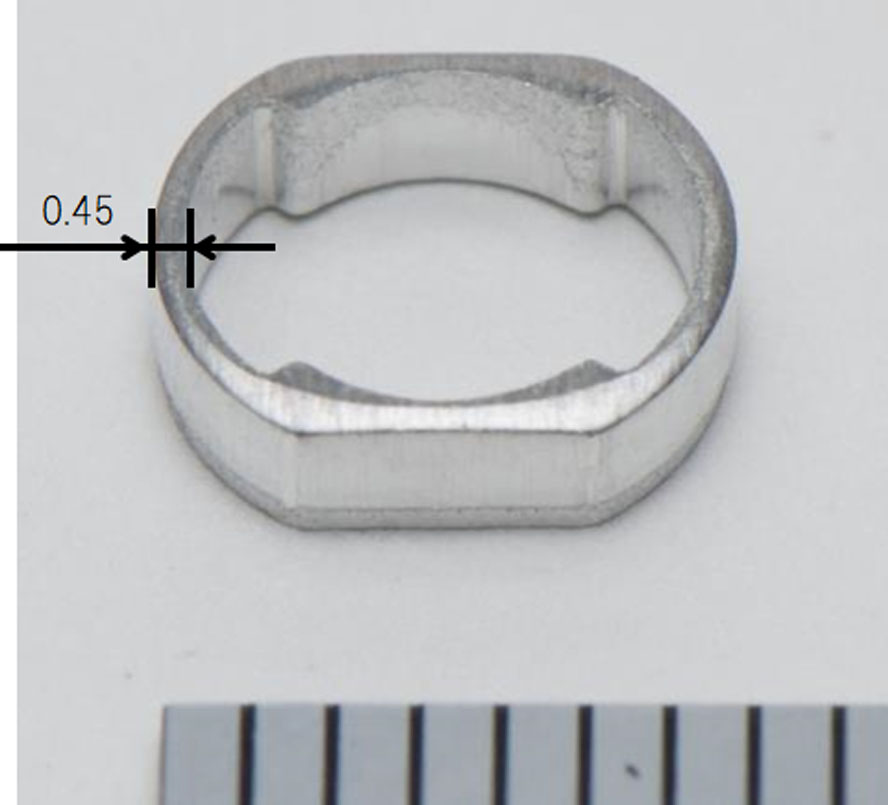
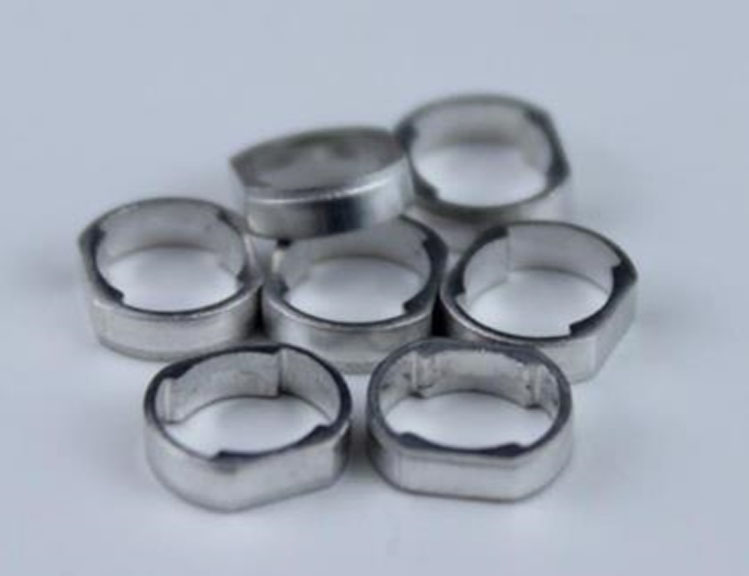
設備 | 60トンクランクプレス |
---|---|
品名 | インサートナット |
材質 | A5052-O |
板厚 | 2.0mm |
2006年
これまでプレス加工では不可能であった、穴径が板厚の半分以下になる細穴抜きに挑戦し、板厚6mmに対し穴径1.2mmの細穴抜きに成功した。
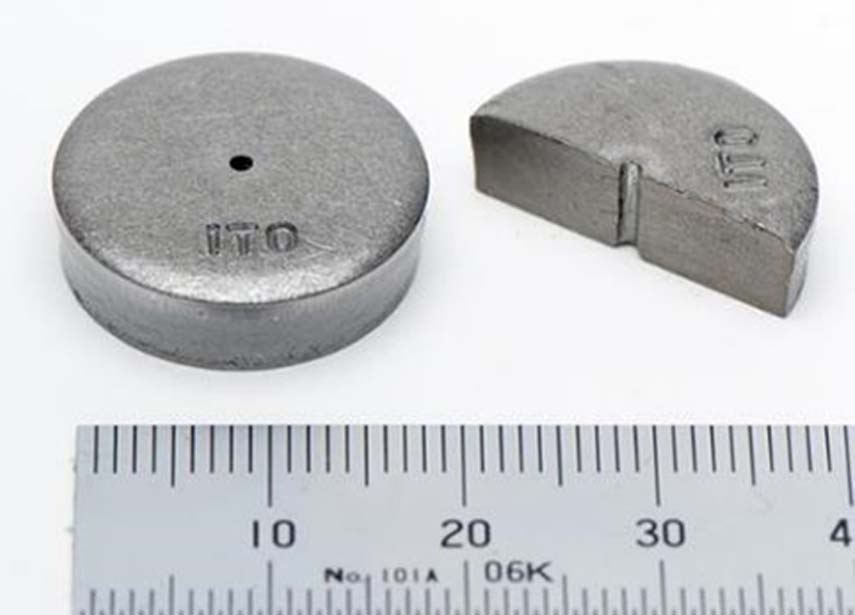
設備 | 45トンクランクプレス |
---|---|
品名 | SPHC |
材質 | 6.0mm |
板厚 | φ1.2 |
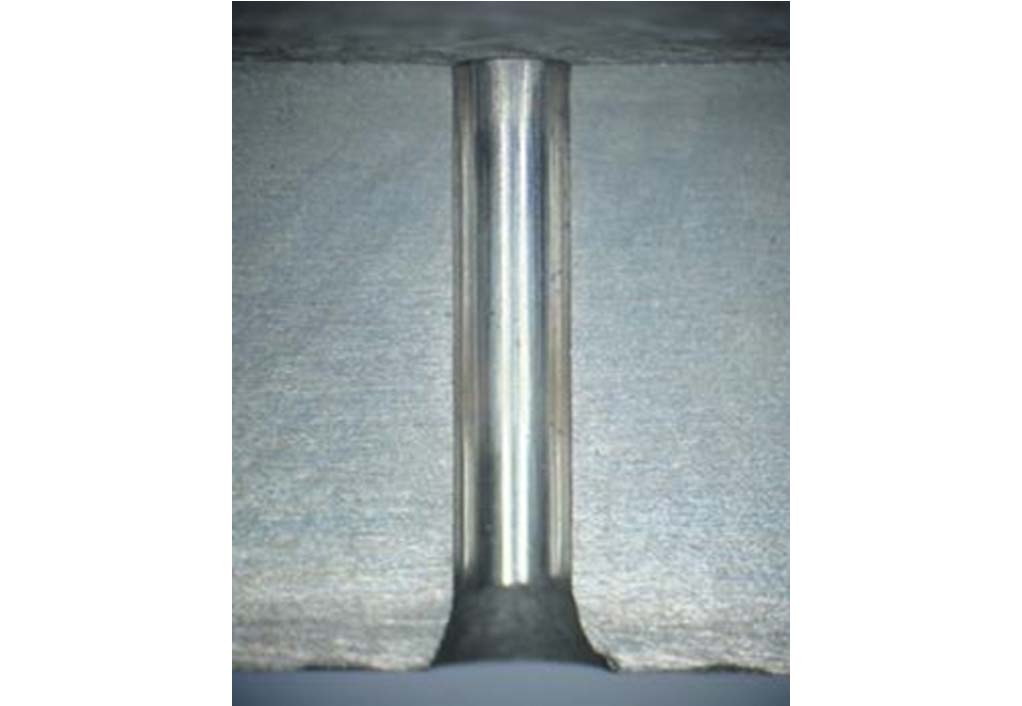
ドリル加工 | ||
---|---|---|
設備 | マシニング | 45tプレス |
工具代 | ¥2,030 | ¥1,410 |
工具寿命 | 250穴 | 35000穴 |
加工時間 | 18秒 | 1秒以下 |
2007年
板厚5.0mmに対して薄い側壁部が巾2.5mmで板厚の50%になる。通常このような打抜きは断面がねじれるが特殊な加工法を開発し、内外径共に75%以上のせん断面を確保。
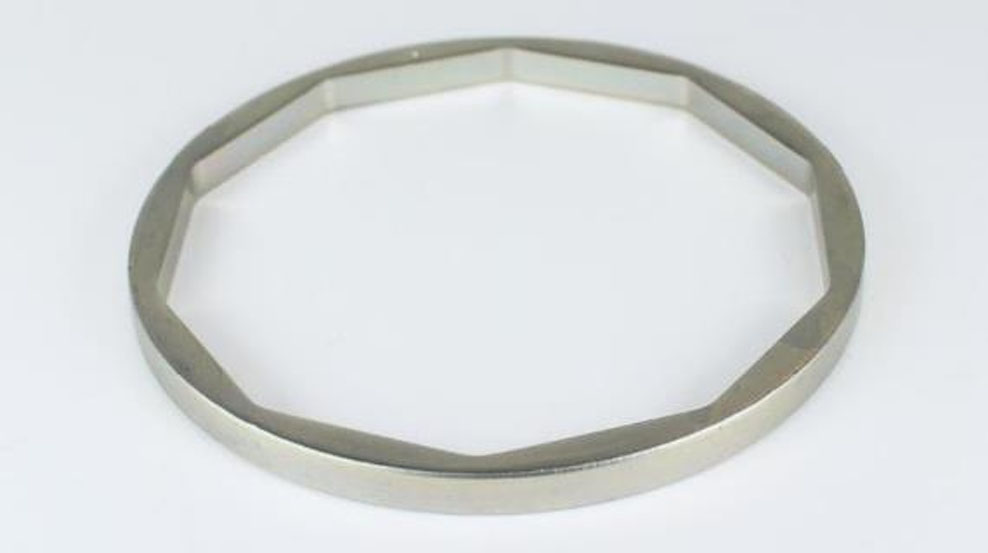
設備 | 300トン高剛性プレス |
---|---|
品名 | ナット・スターター |
材質 | SPH270C |
板厚 | 5.0mm |
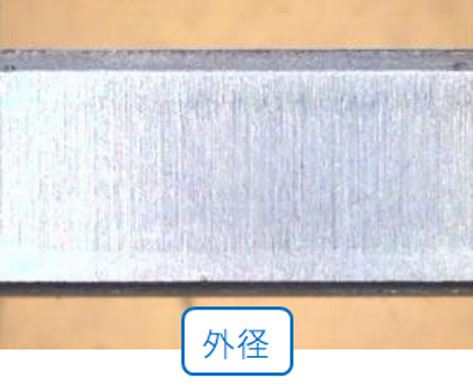
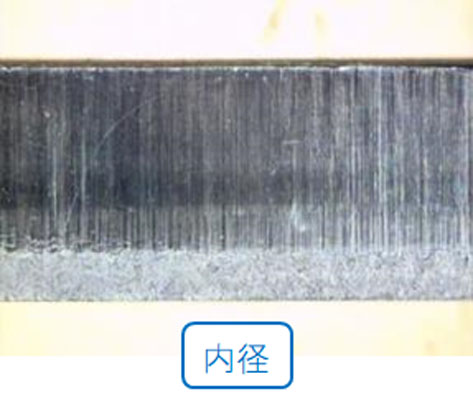
2012年
従来はファインブランキングで生産していたシートリフター用セクターギアを順送りプレス加工に工法転換。従来工法では板厚6mに対し1.5mm以上あった歯先ダレを0.5mm以下に抑え、せん断面長さ90%を確保。
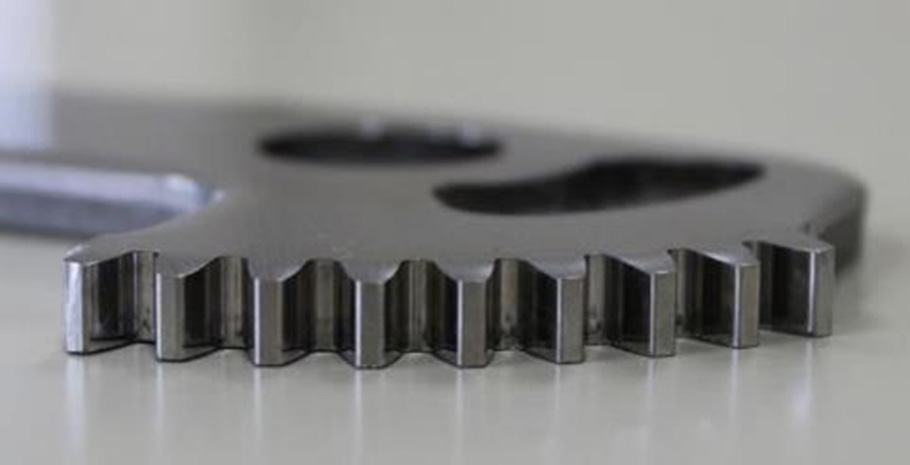

当社の順送プレス品
板厚 6.0mm
ダレ 0.5mm
板厚の10%以下
設備 | 300トンナックルリンクプレス |
---|---|
品名 | セクターギア |
材質 | SCM415 |
板厚 | 6.0mm |
2014年
細い半島形状の輪郭にマッチングを設けず、ダイ強度を維持したまま一筆書き打抜きが可能。工程数の削減と打抜き精度が向上。
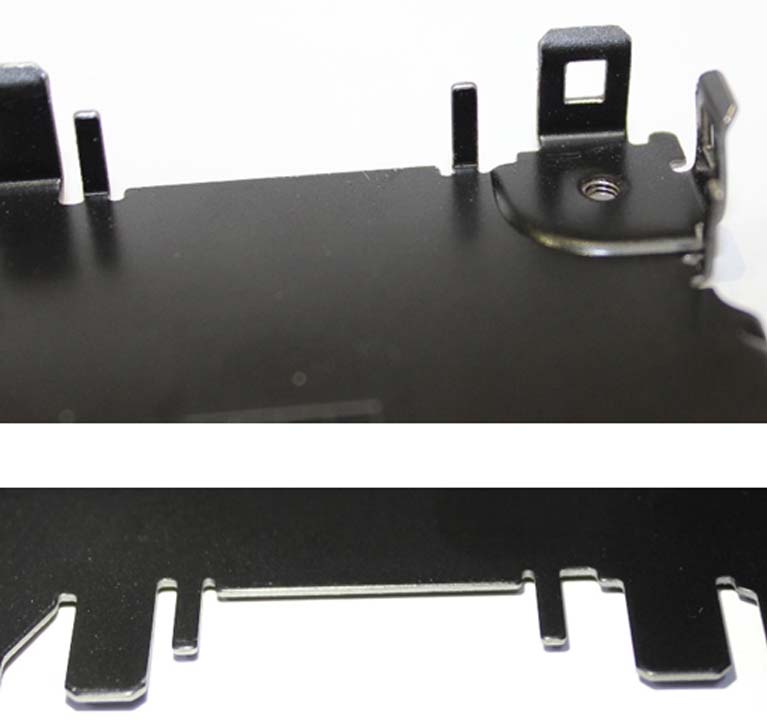
設備 | 110トンプレス |
---|---|
品名 | ベース |
材質 | SECC(放熱塗装材) |
板厚 | 0.8mm |
2016年
顧客からの精密せん断加工ニーズは次第に厚い材料へ適用され、板厚7.2mm精密せん断に成功した。小穴を全てプレスで精密に仕上げ面押しすることにより、後工程の旋削時間を大幅に短縮した。
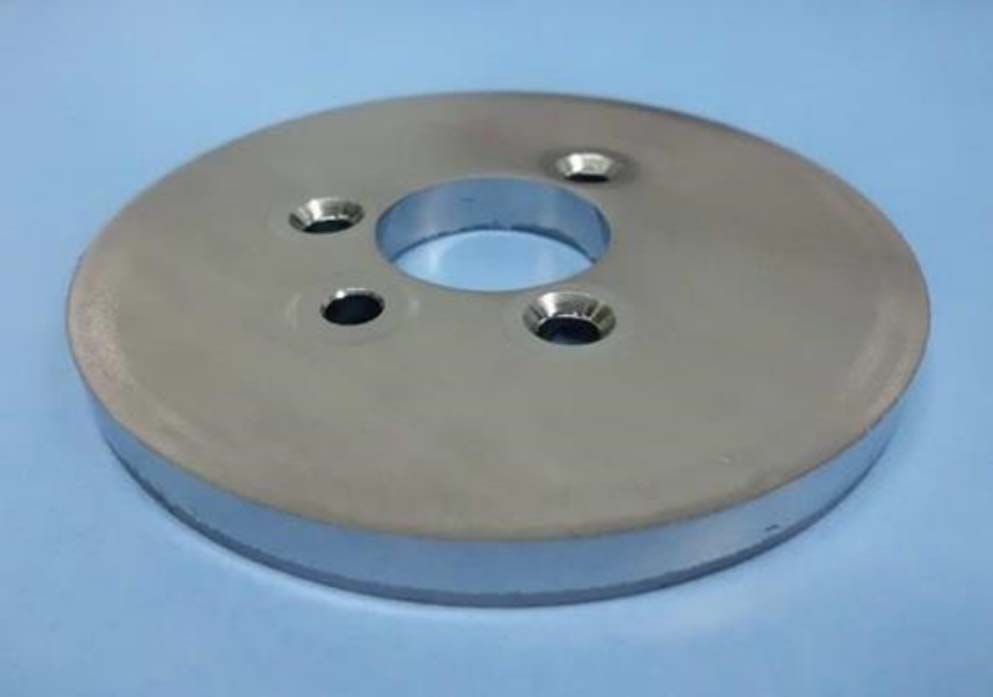
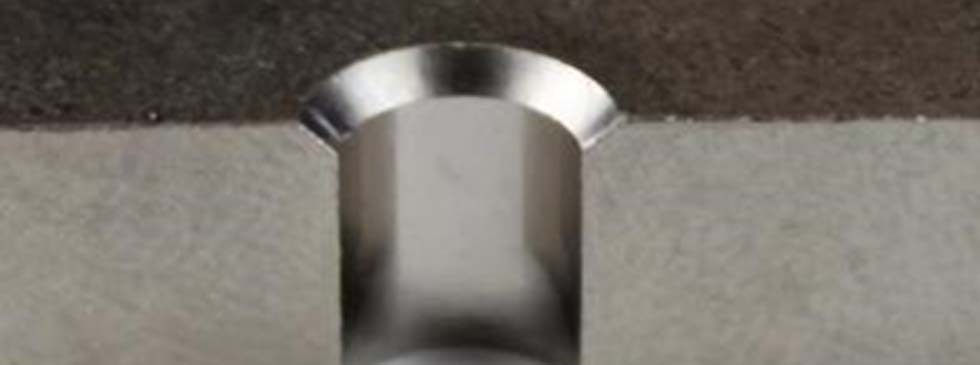
設備 | 400トンナックルリンクプレス |
---|---|
品名 | 基材 |
材質 | SPH440C |
板厚 | 7.2mm |
2020年
従来はファインブランキングで生産していたシートリフター用セクターギアを順送りプレス加工に工法転換。歯先ダレを0.2mm以下に抑え、せん断面長さ90%以上を確保。
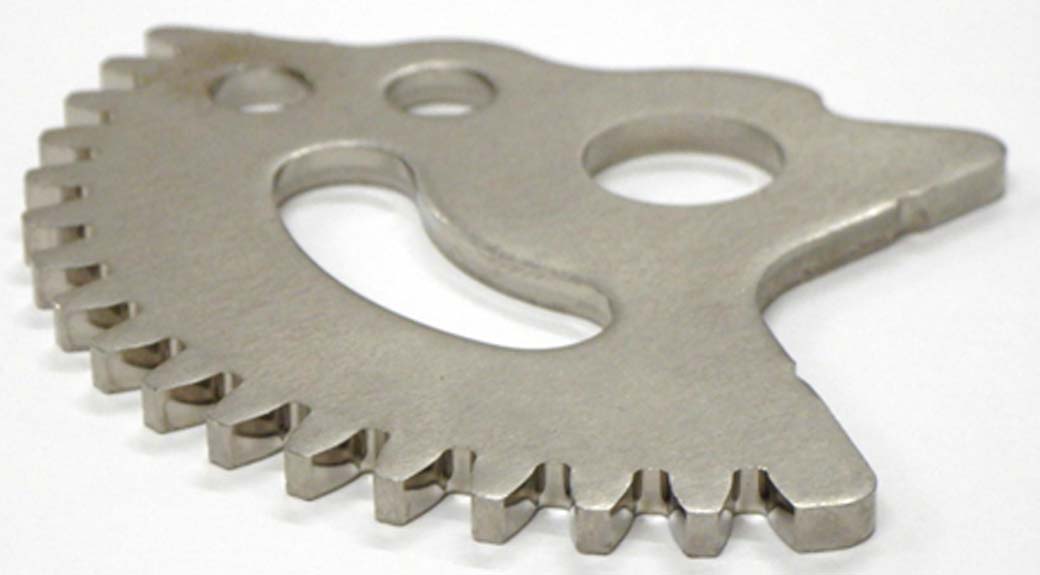
設備 | 200トンサーボプレス |
---|---|
品名 | セクターギア |
材質 | SAPH440 |
板厚 | 3.2mm |
モジュール | 2 |
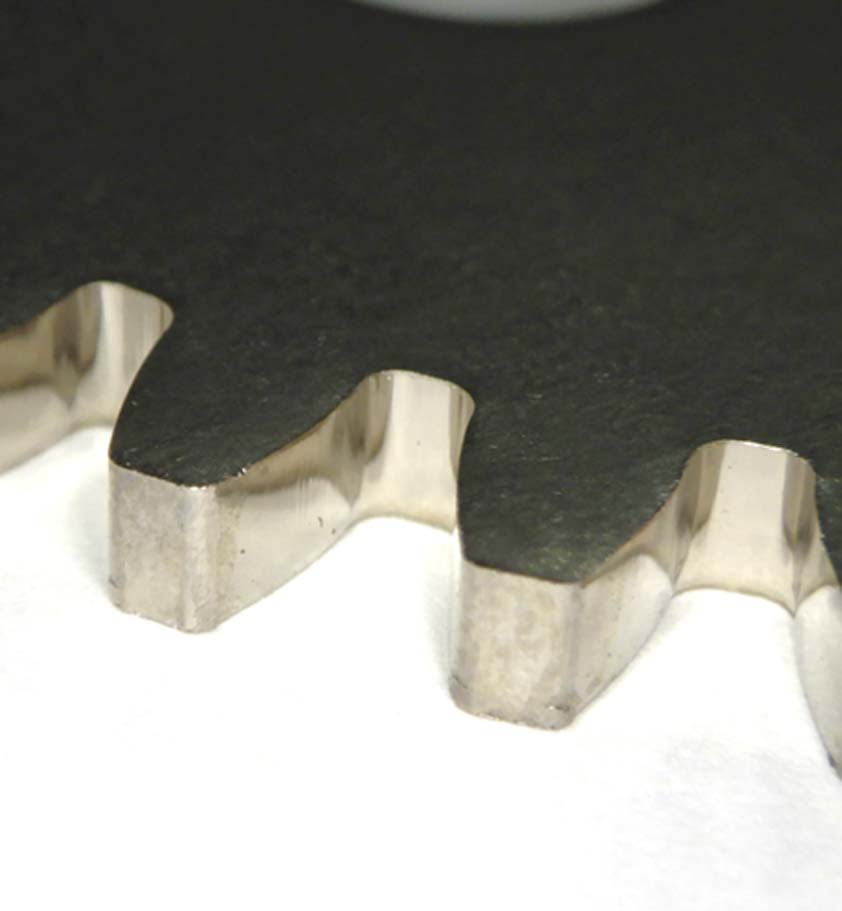
曲げ技術
1999年
Windows 95 の普及と共に超大量生産が始まったフロッピーディスクドライブのローターヨークのプレス量産化に成功。軸径公差や振れ・平面度など5ミクロンの精度が要求されたため、金型部品の寸法精度はサブミクロンで仕上げた。
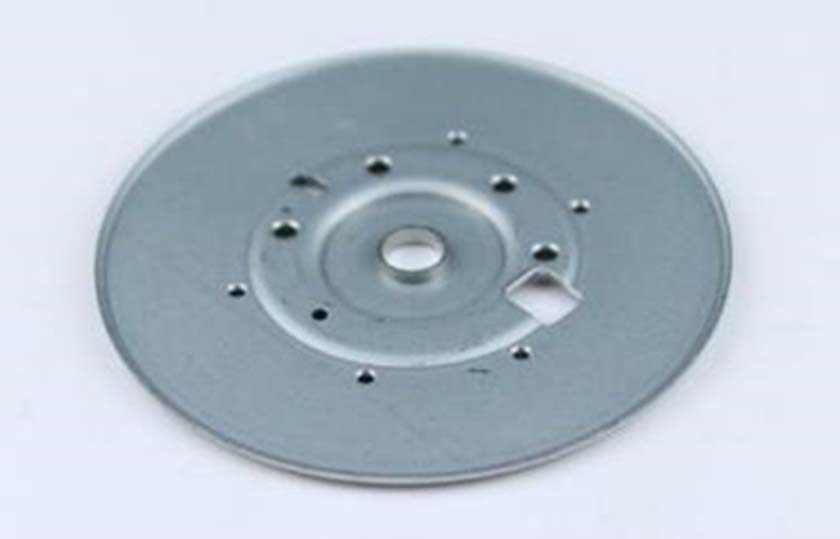
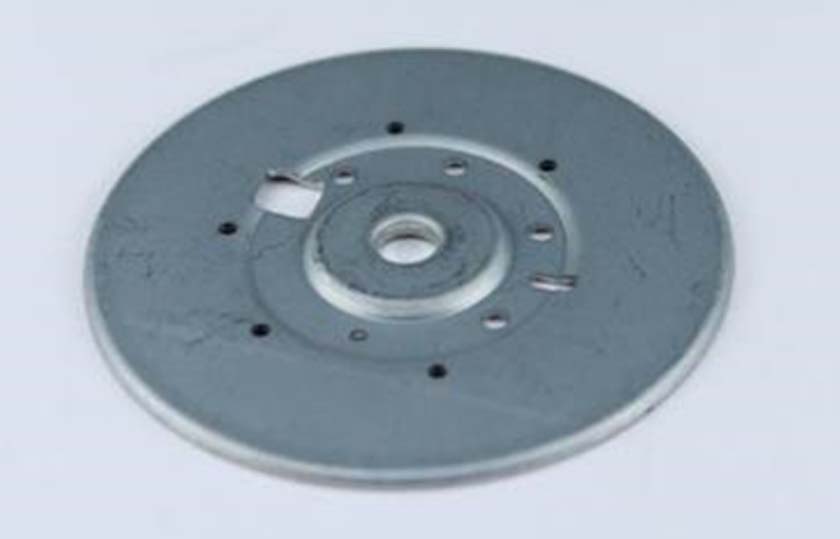
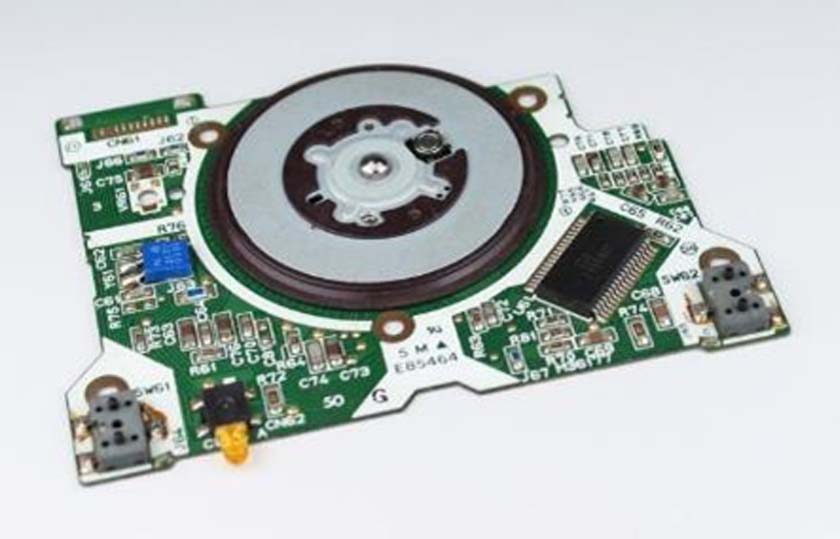
設備 | 110トン高速プレス |
---|---|
品名 | ローターヨーク |
材質 | EGC-E20/20 |
板厚 | 0.6mm |
2009年
板材を切断せずに重ね合わせる技術でキーホルダーの順送りプレス加工に成功。
また、板厚1.6mm対しφ0.5の細穴加工を行っている。
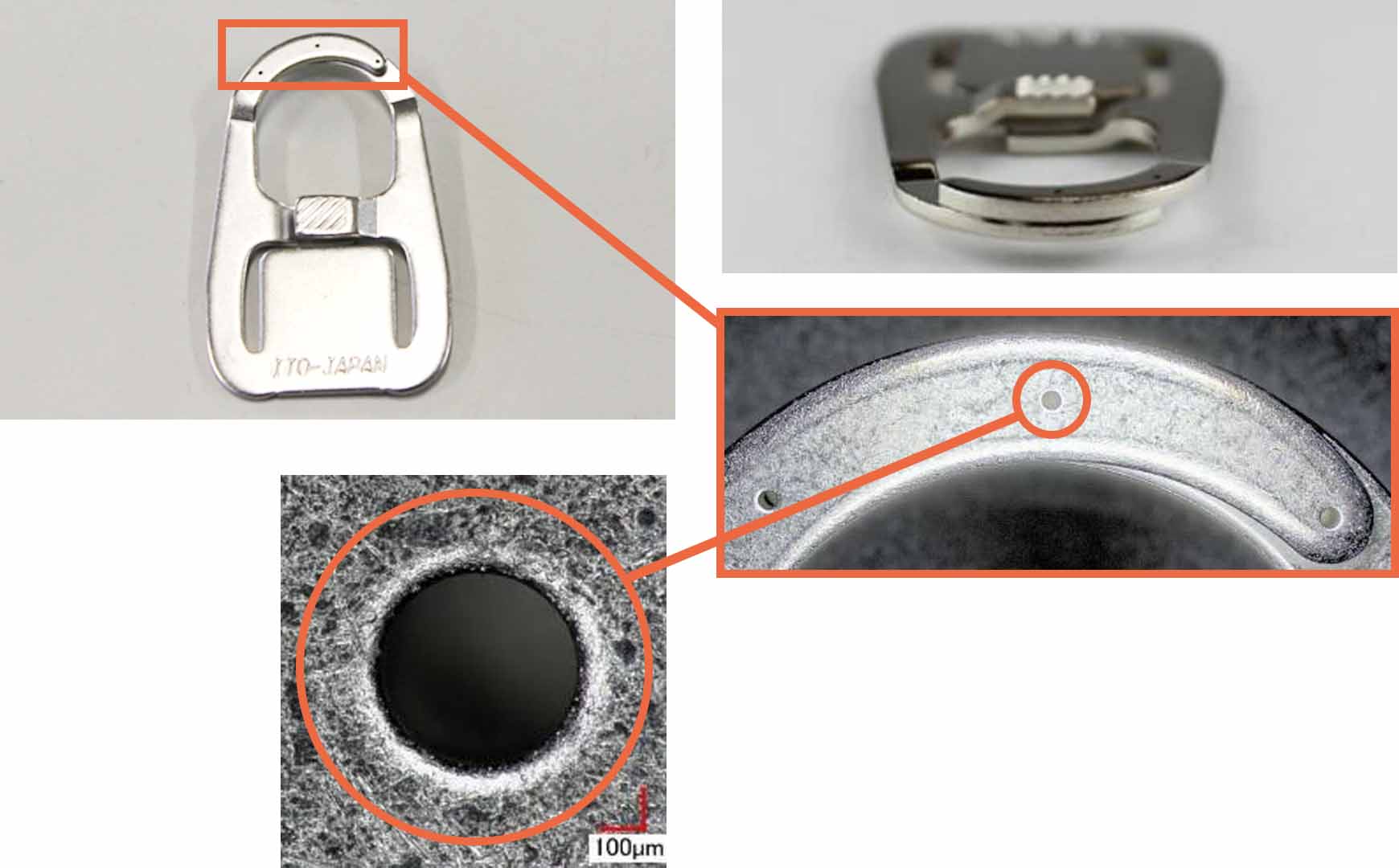
設備 | 100トン高速プレス |
---|---|
材質 | C2680-1/2H |
板厚 | 1.6mm |
2017年
BEFORE:クランクプレスではスプリングバックがばらつき、材料が変わると修正工程の調整が必要だった。
AFTER:サーボプレスで曲げ過程での減速と、下死点で0.2秒停止することでスプリングバックのバラツキを押え込むことに成功した。
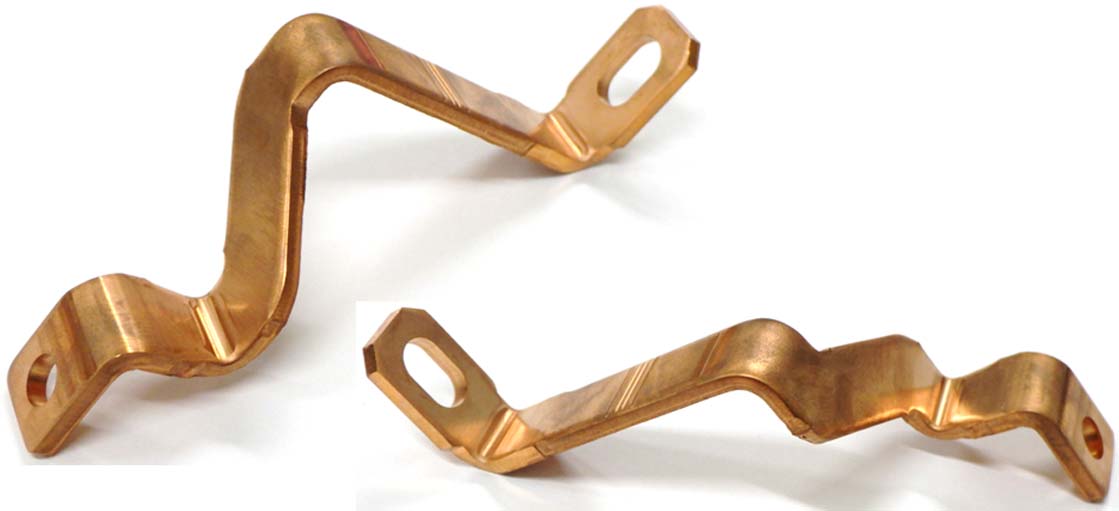
設備 | 200トンサーボプレス |
---|---|
品名 | バスバー |
材質 | C1020-H |
板厚 | 3.0mm |
絞り技術
1995年
ステンレスの角絞り部品。7工程で16×8×高さ50に絞っている。
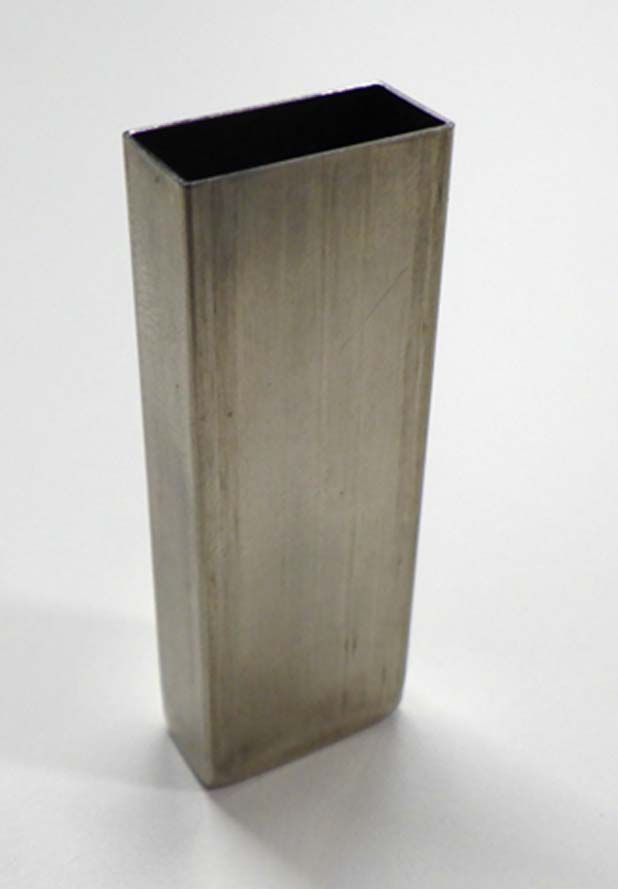
設備 | 110トンプレス |
---|---|
品名 | バッテリーケース |
材質 | SUS304 |
板厚 | 0.4mm |
2003年
シートリフタークラッチの外輪部品。浸炭焼入れ焼戻し後の内径寸法を±0.02で管理。
1社を除く全ての日系自動車メーカーで採用。2017年に累計生産1億台を記録。
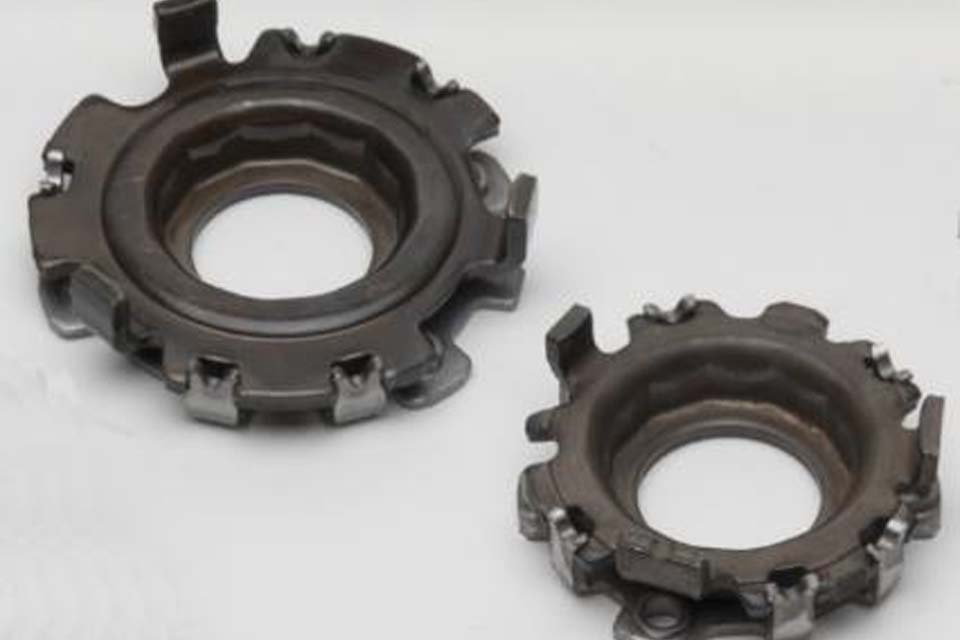
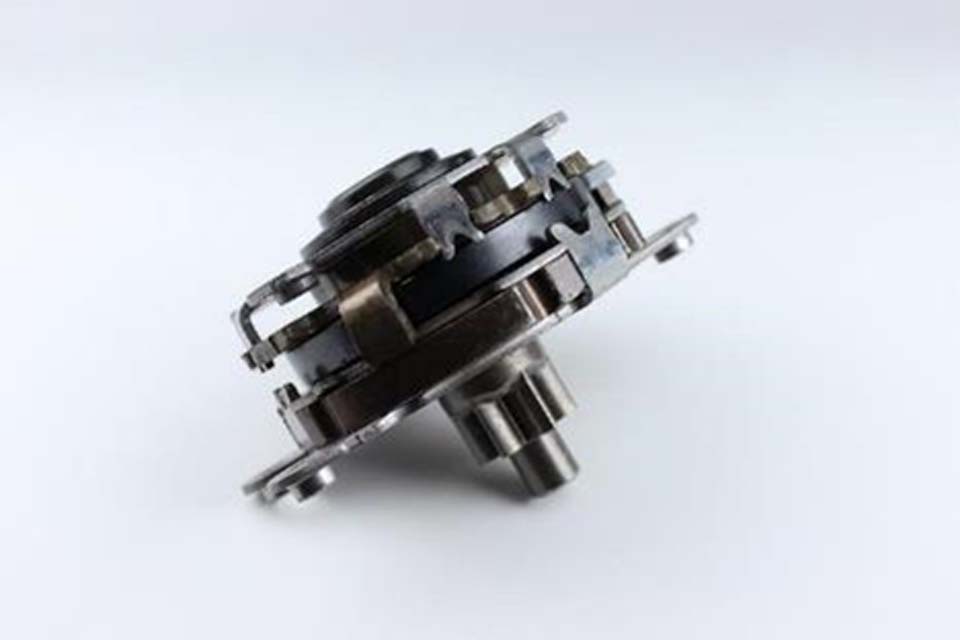
設備 | PMX-3000 |
---|---|
品名 | 外輪 |
材質 | SCM415 |
板厚 | 2.9mm |
2015年
ステンレスの深絞り部品。品質要求上、出来るだけ局部的な変形を避けて均質になる様に工程上の工夫をしている。
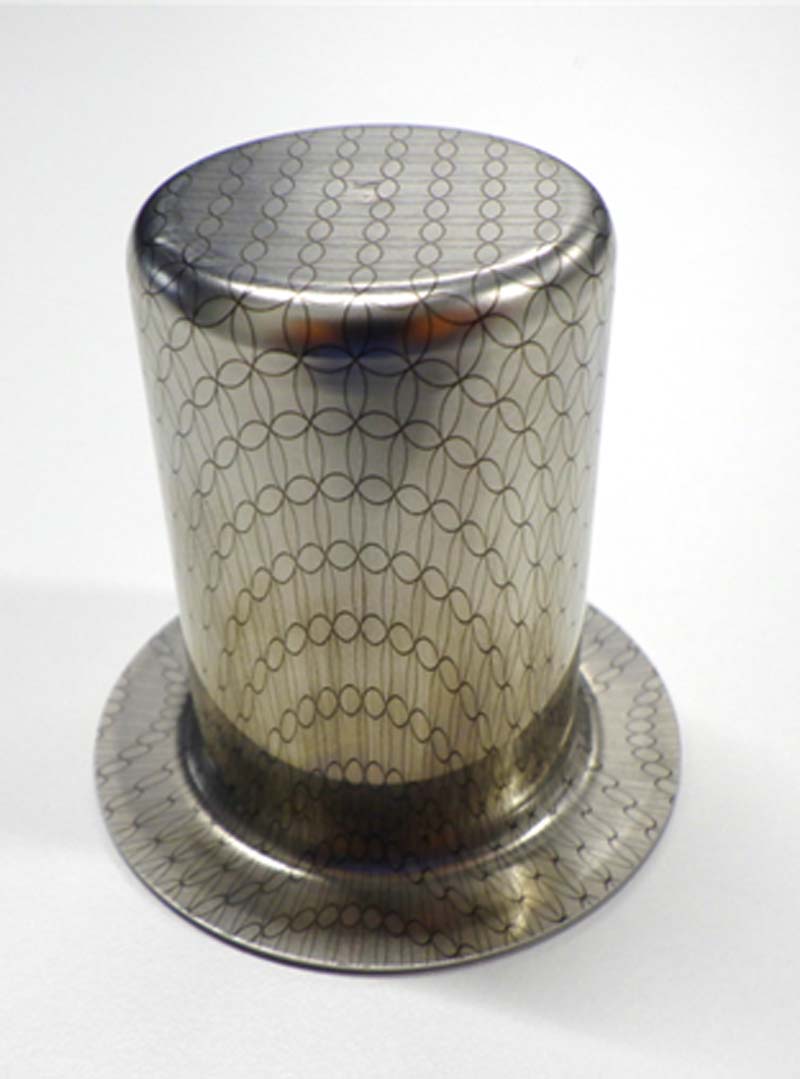
設備 | 150トンサーボプレス |
---|---|
品名 | ケース |
材質 | SUS304 |
板厚 | 0.5mm |
2020年
シートリフタークラッチのケース。ハイテン材の精密絞り。
金型は24工程あり、長さは2300mm。
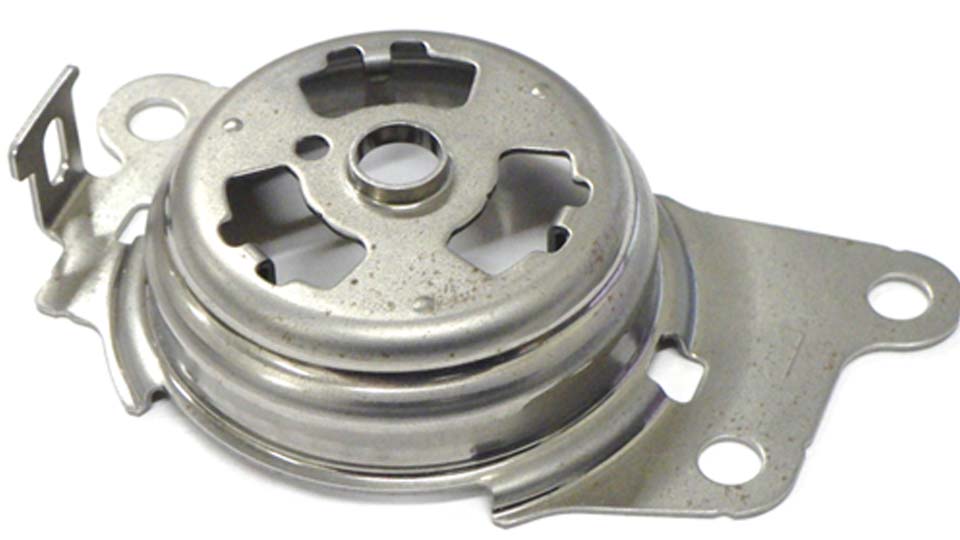
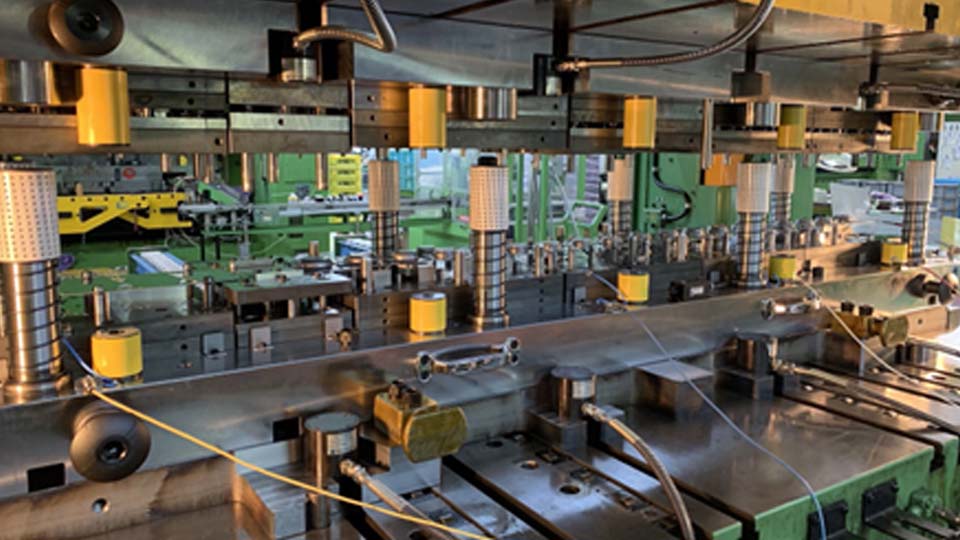
設備 | PMX-6000 |
---|---|
品名 | ケース |
材質 | SPC590 |
板厚 | 1.0mm |
板鍛造
1995年
現在の日本では広く普及している板鍛造や精密せん断と呼ばれる技術を当社では1990年代から既に順送り金型に織り込み量産していた。
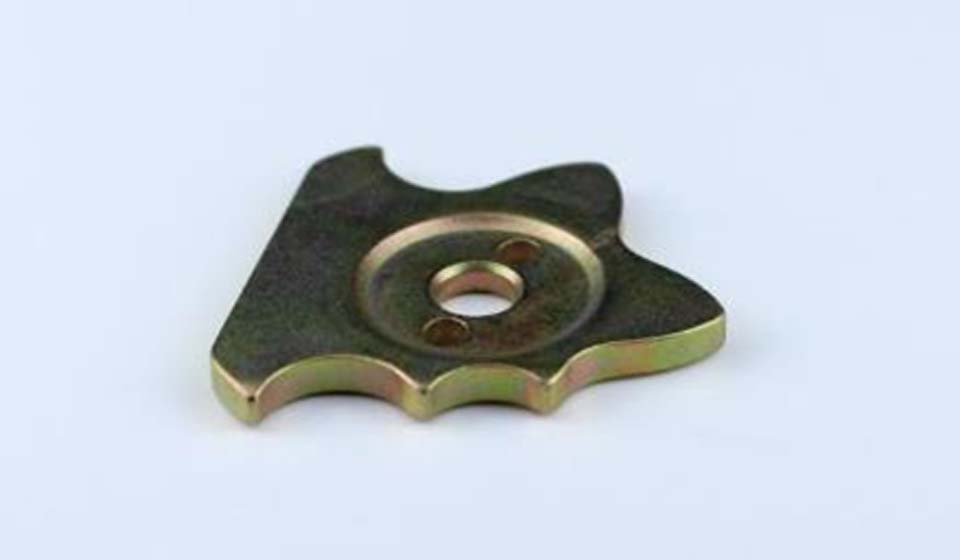
設備 | 150トンリンクプレス |
---|---|
品名 | シフトドラム |
材質 | SPCE |
板厚 | 3.2mm |
2008年
これまでに培ったきた板鍛造技術を応用し、底突のセレーション、ナットの一体成形を順送りプレス加工で実現した。
得意としている細穴加工も順送り金型内で4ヶ所同時加工を行っている。
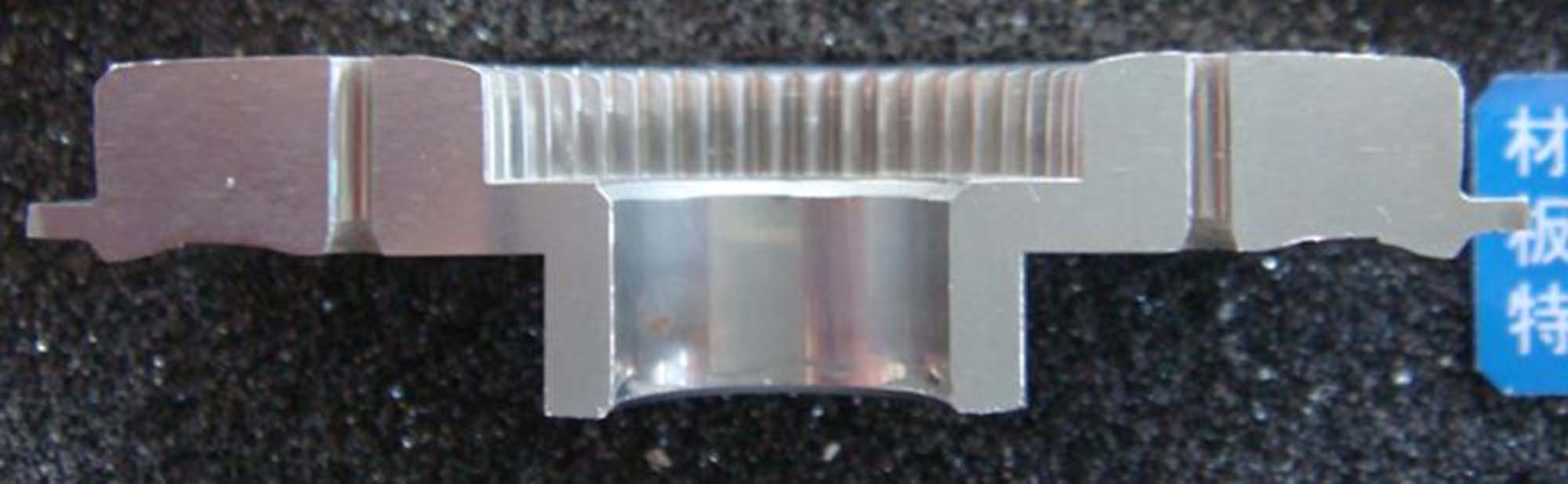
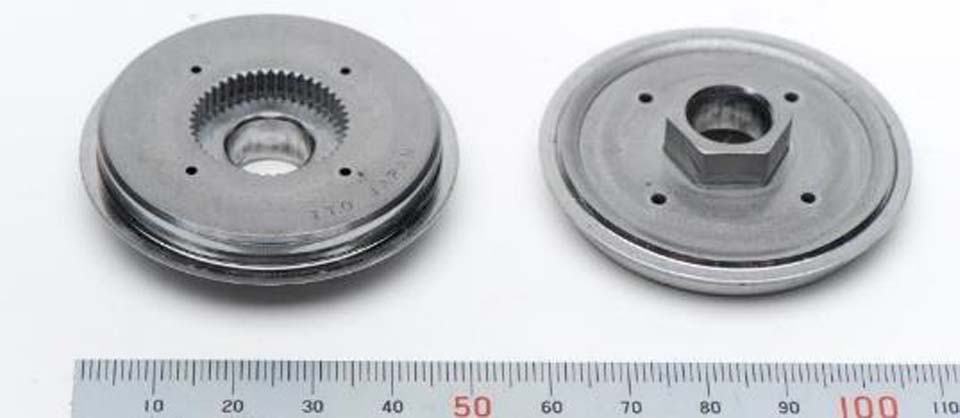
設備 | 600トンリンクプレス |
---|---|
材質 | SPHC |
板厚 | 6.0mm |
2010年
これまで当社はせん断技術による細穴加工を得意としてきたが、新たにせん断技術と板鍛造技術を組合せる事で、よりアスペクト比の高い細穴加工に成功した。
前者は板厚6mmに対しφ1.2であったが、後者は高さ7mmに対しφ1.15を実現。
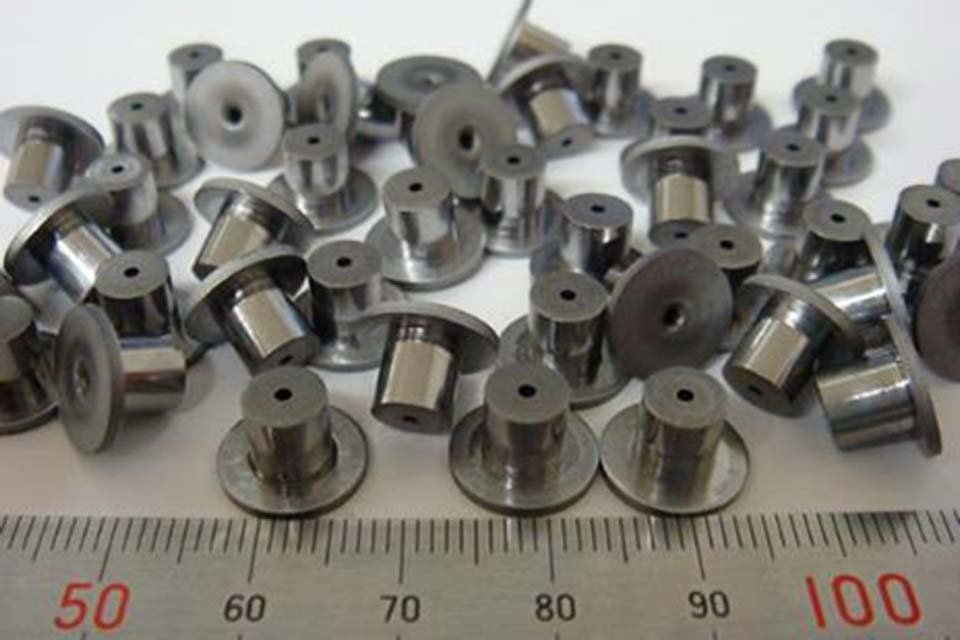
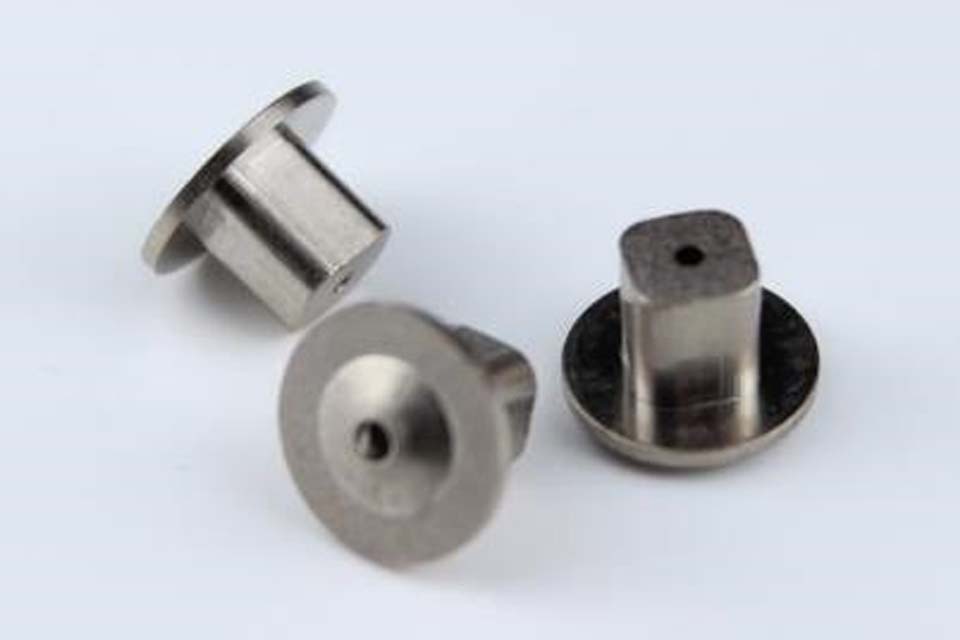
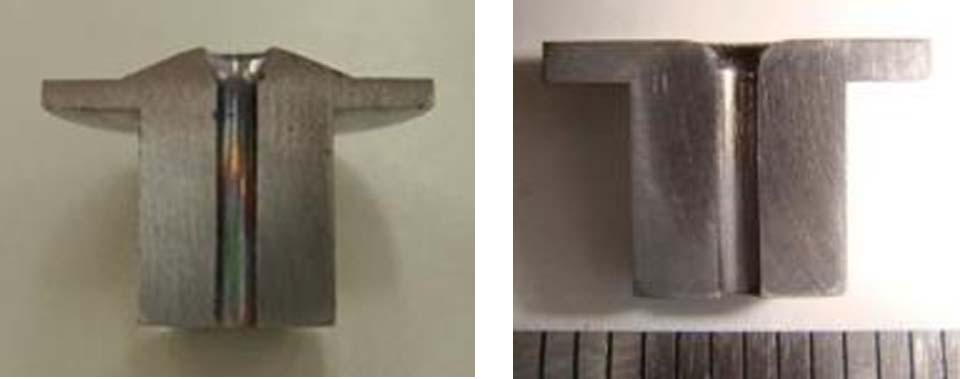
設備 | 150トンサーボプレス |
---|---|
品名 | ノズル |
材質 | SPHC |
板厚 | 5.0mm |
2011年
カーエアコンクラッチ部品のリベット一体成形を順送りプレスで量産化に成功した。
Φ3.0, 高さ5mmのピンを板鍛造で成形、精密せん断技術を駆使し、板厚4.3mmに 対し巾2mmのスリット抜きや外径せん断面80%以上を実現。
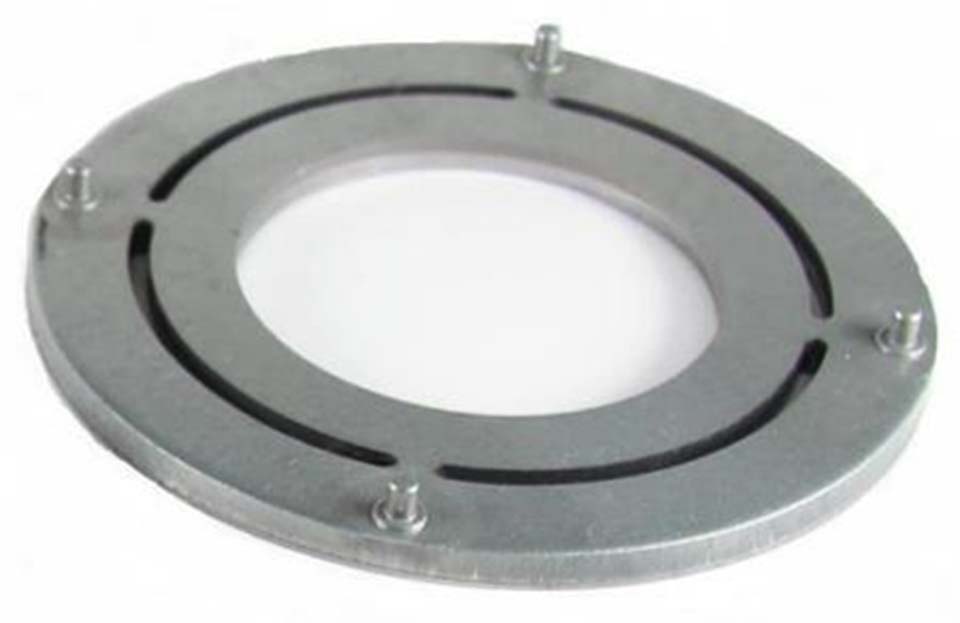
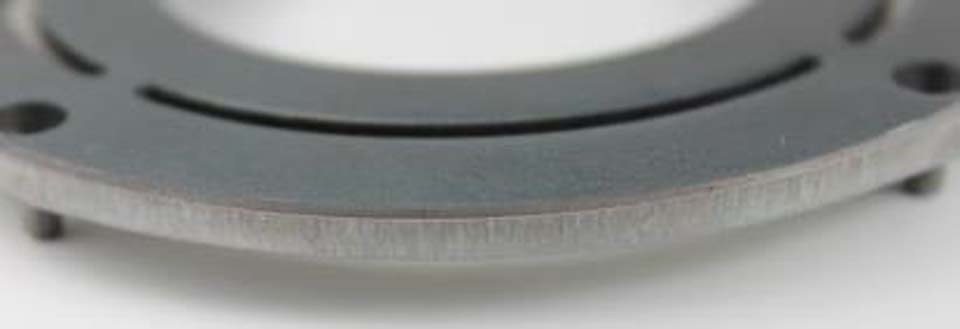
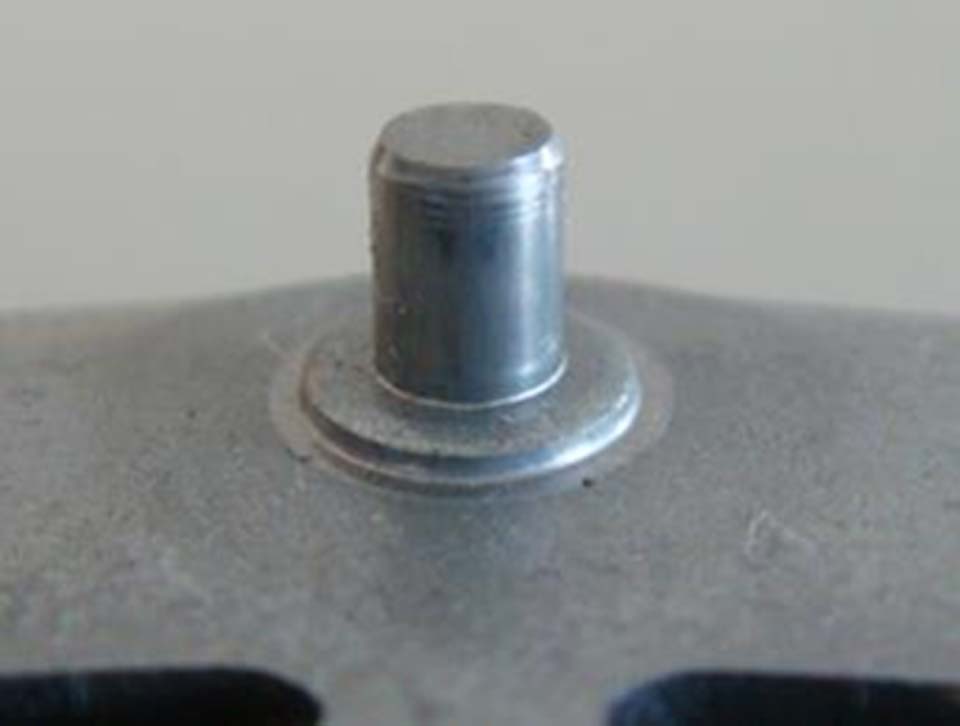
2011年
抜き穴上下面の精密な形状作りこみに成功。
R0.7部と接触するボールで油をシールする必要があるため面粗さはRa0.3以下で管理、ボールをのせた際の高さ公差は±0.01を維持しながら月産100万個以上。
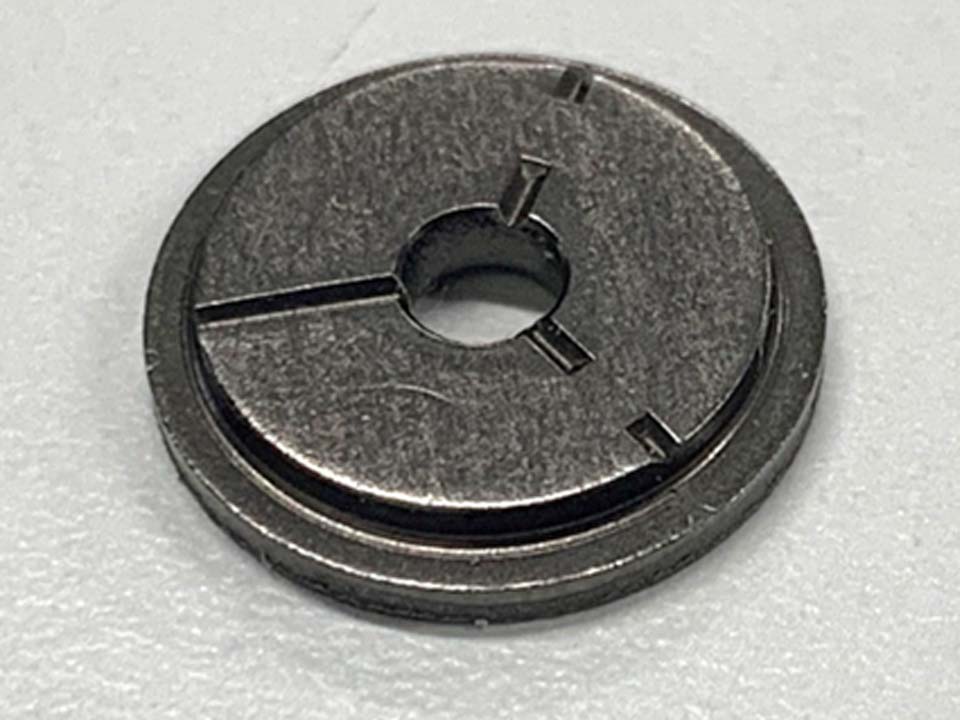
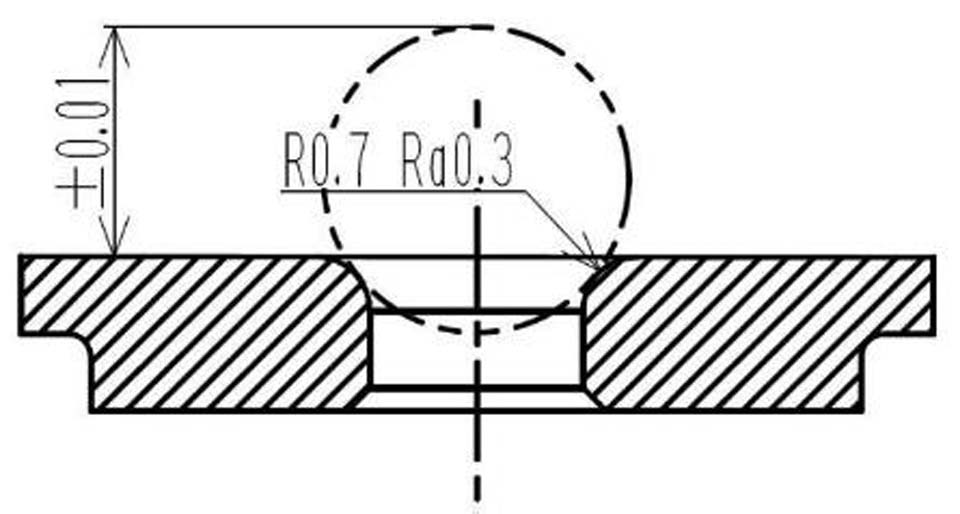
設備 | 110トンプレス(2個取) |
---|---|
品名 | ボールシート |
材質 | SPHC |
板厚 | 2.0mm |
2012年
これまで困難であった表裏両面からの同時加工に成功。
両面からの公差があり、板厚のばらつきに左右される。
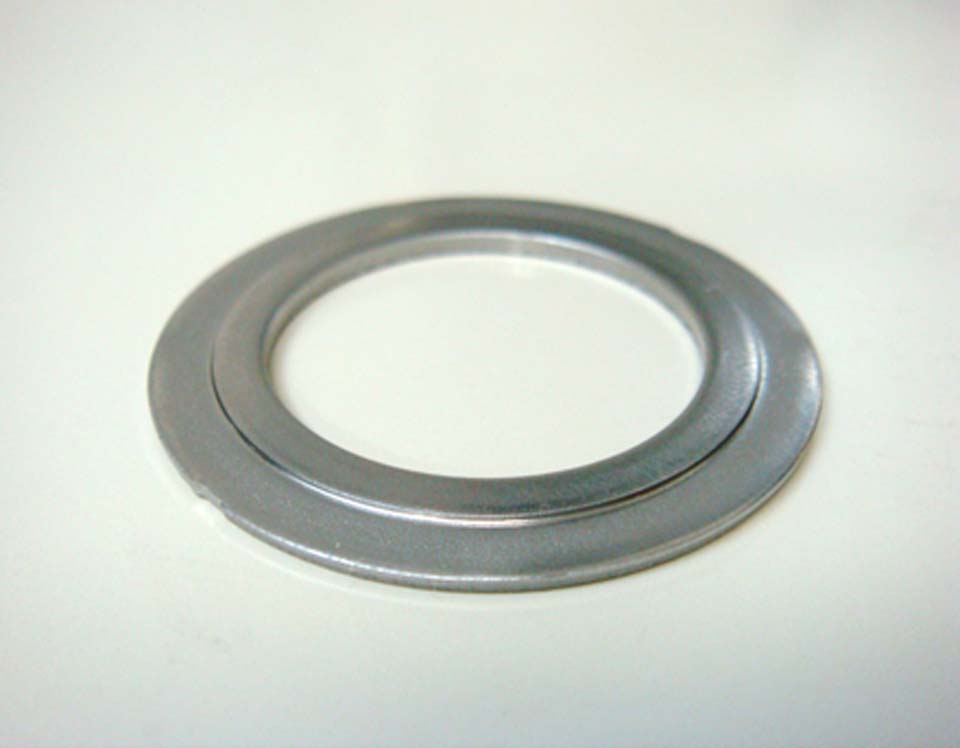
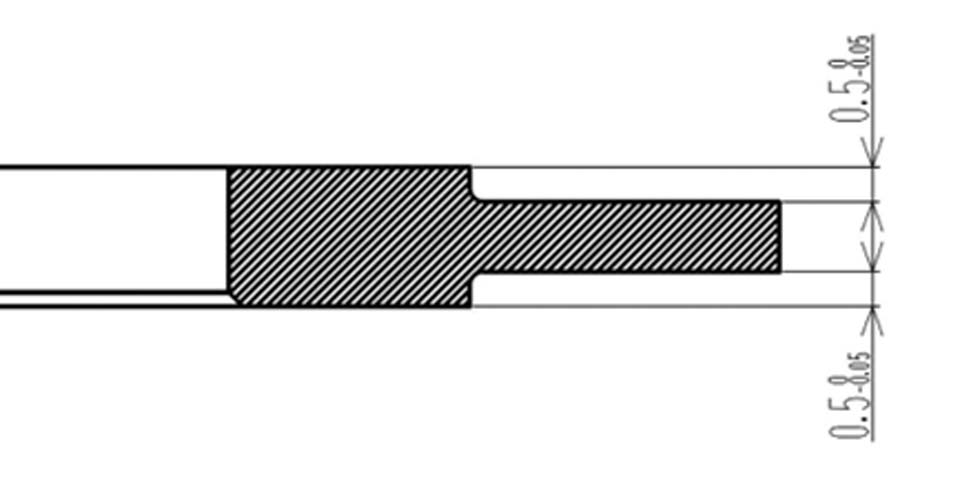
設備 | 200トン高剛性プレス |
---|---|
品名 | 段付ワッシャー |
材質 | SPCC |
板厚 | 2.0mm |
2018年
バーリング形状であるが自然R不可のため、板鍛造で成形した。
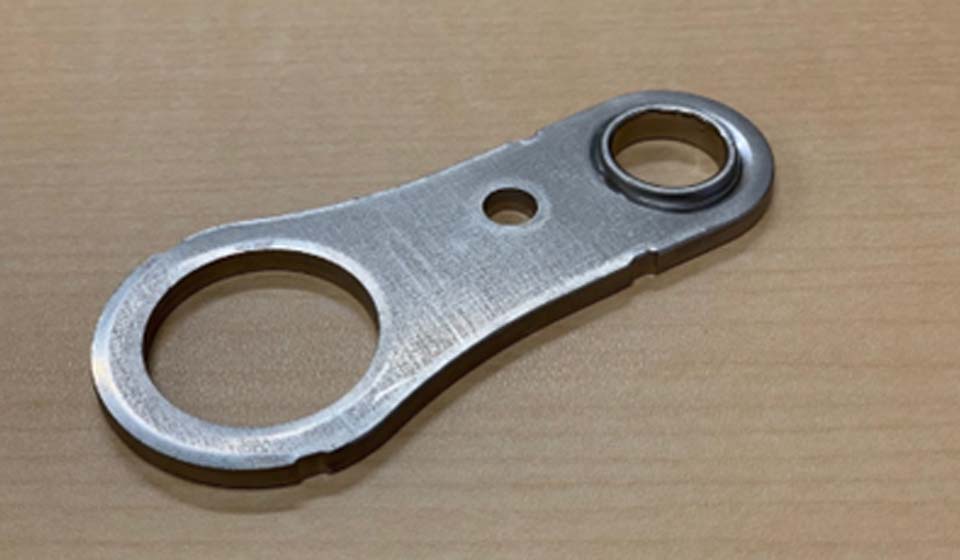
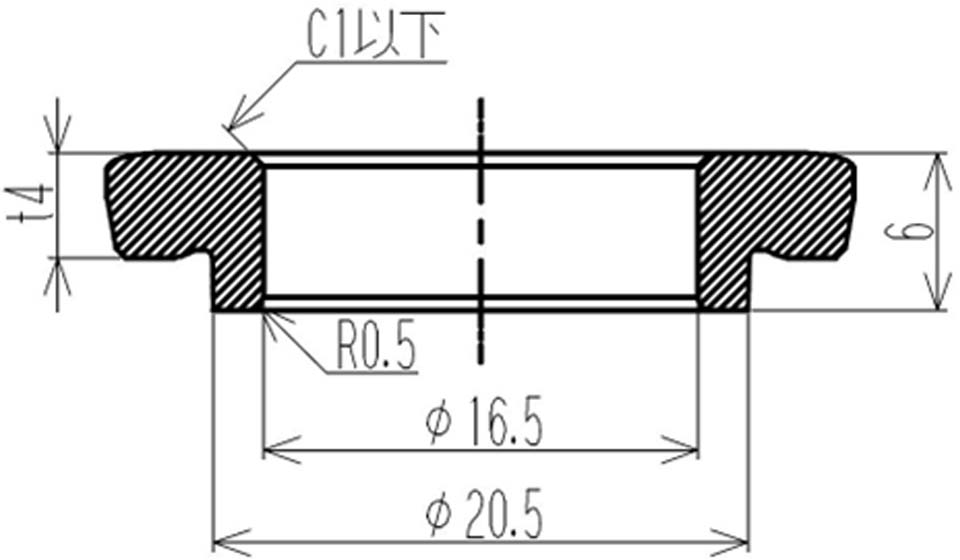
設備 | 400トンリンクプレス(2個取り) |
---|---|
品名 | LINK, VERTICAL |
材質 | SPH440-OD |
板厚 | 4.0mm |
システム開発事例
2015年
プレス連続印字システム
レーザーマーカーを利用した連続印字システム。得られた情報や1個単位の識別番号を製品に直接レーザーマーキングすることで、これまでロット単位、箱単位だったトレーサビリティーが1個単位まで追跡可能。
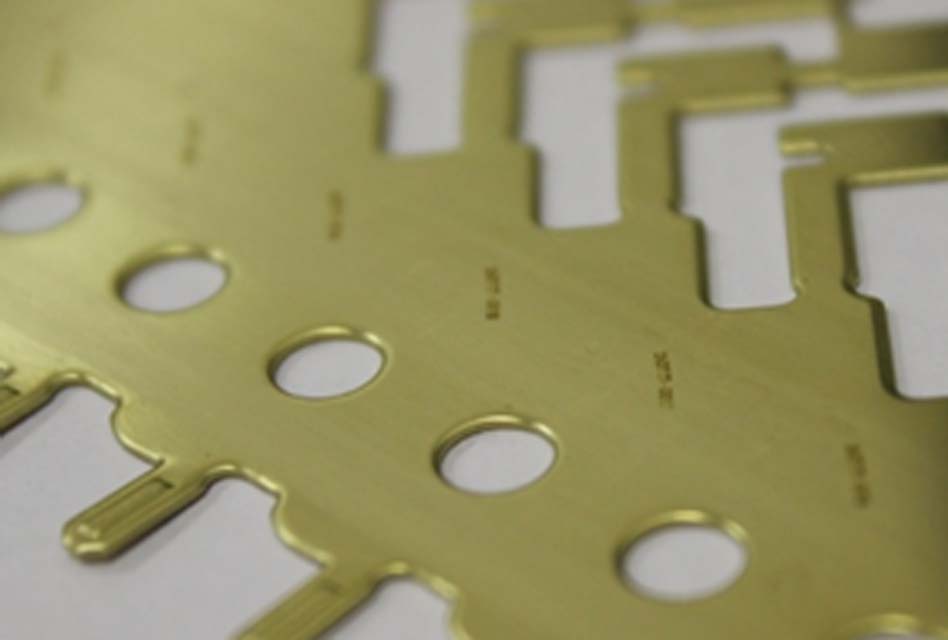
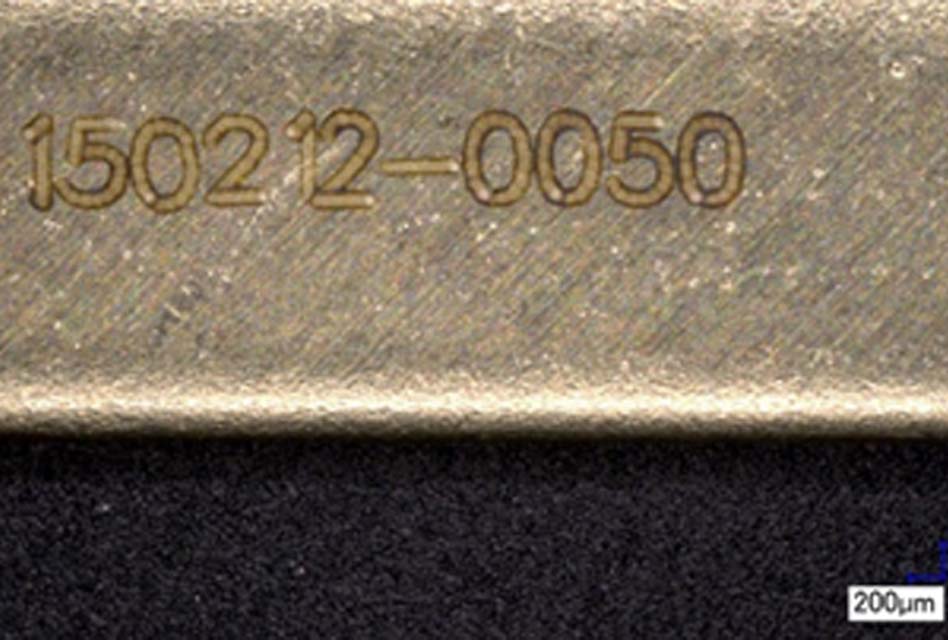
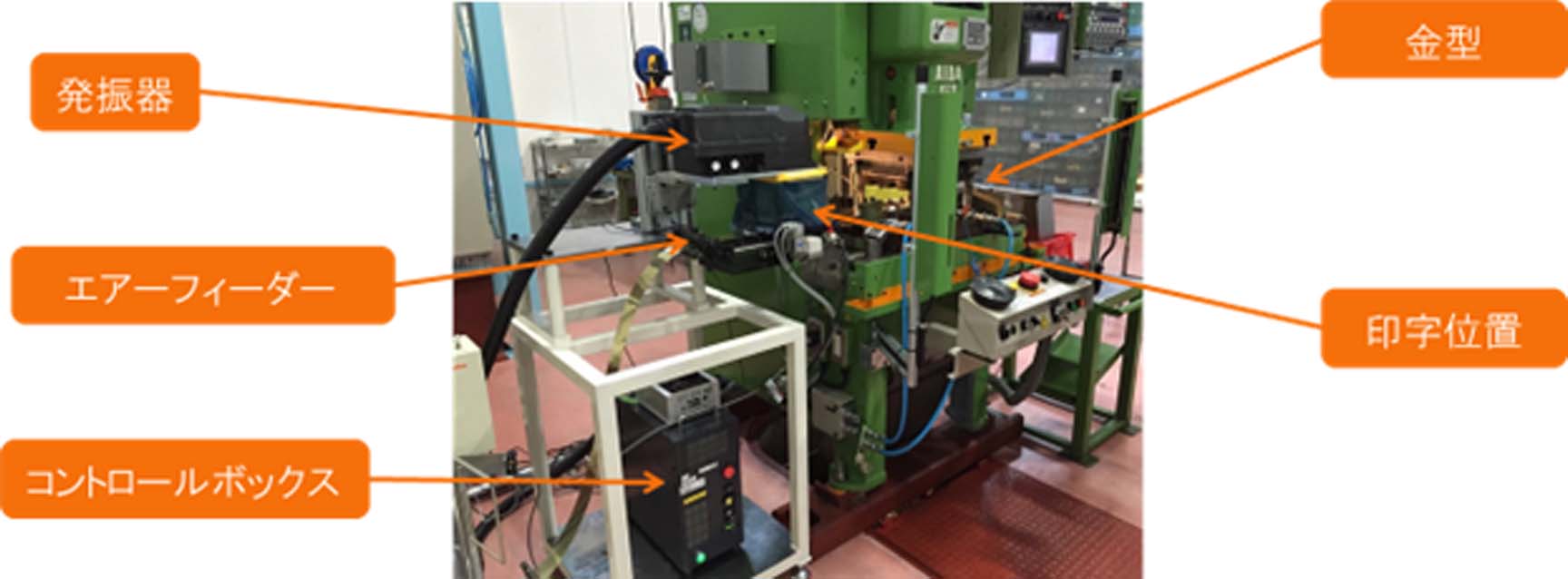
2016年
スクライブドサークルマーキングシステム
レーザーマーカーを利用したスクライブドサークルデータ作成システム。
これまでは金属インクをスタンプして作成していたスクライブドサークルをレーザーマーカーで描くことにより多工程でも線が消えず、精密な測定が可能になった。
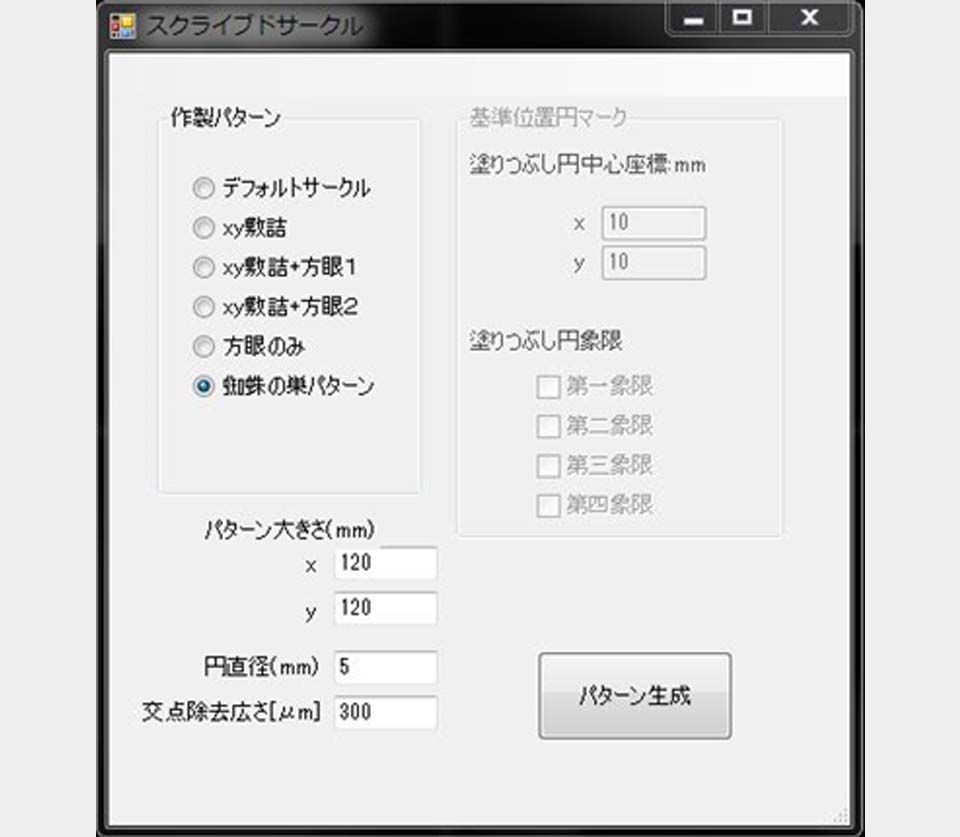
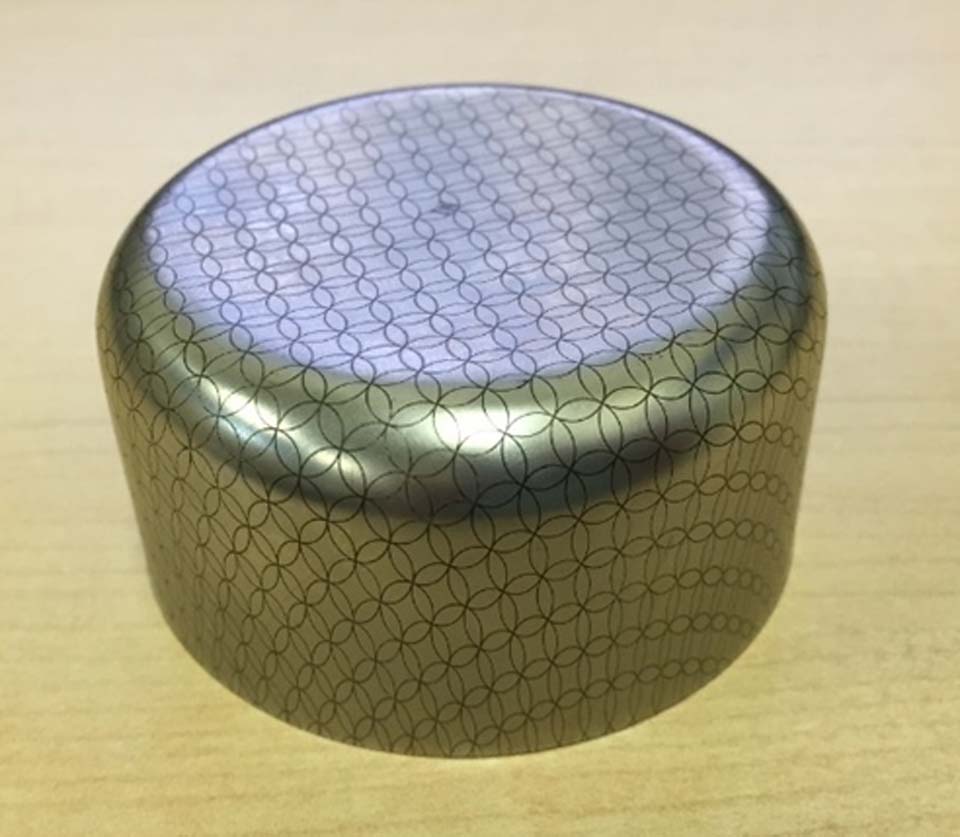
2020年
プレス加工センシングシステム
稼働中の金型をエッジPCで常時監視(センシング)及び処理を行いクラウドへ同時転送。傾向値管理とAiによるパンチ寿命予測システム。
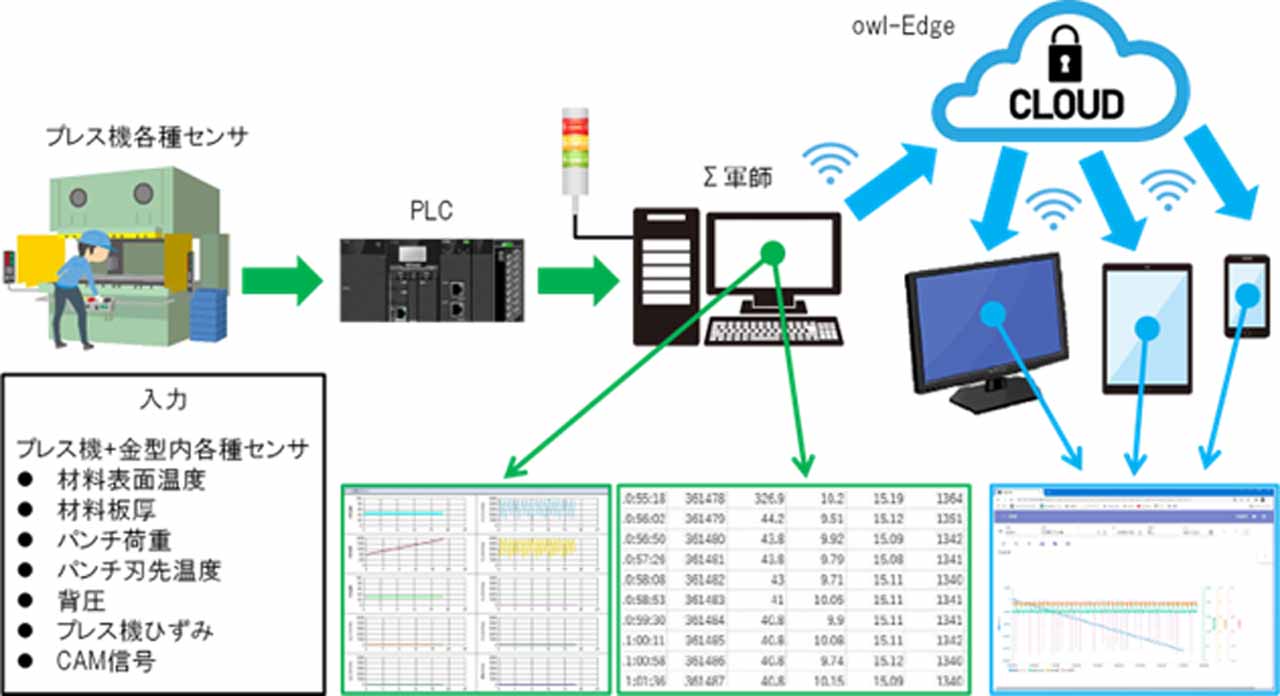
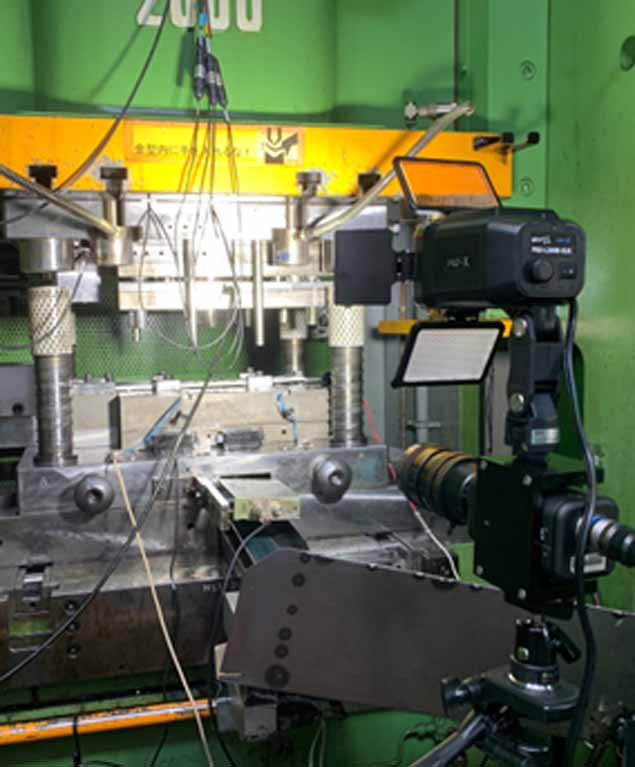
2022年
PRMS SHOT (Press Remote Monitoring System)
ラズベーリーパイを利用したプレス機の稼働監視及び異常発生時のドラレコ機能とロギングシステム。
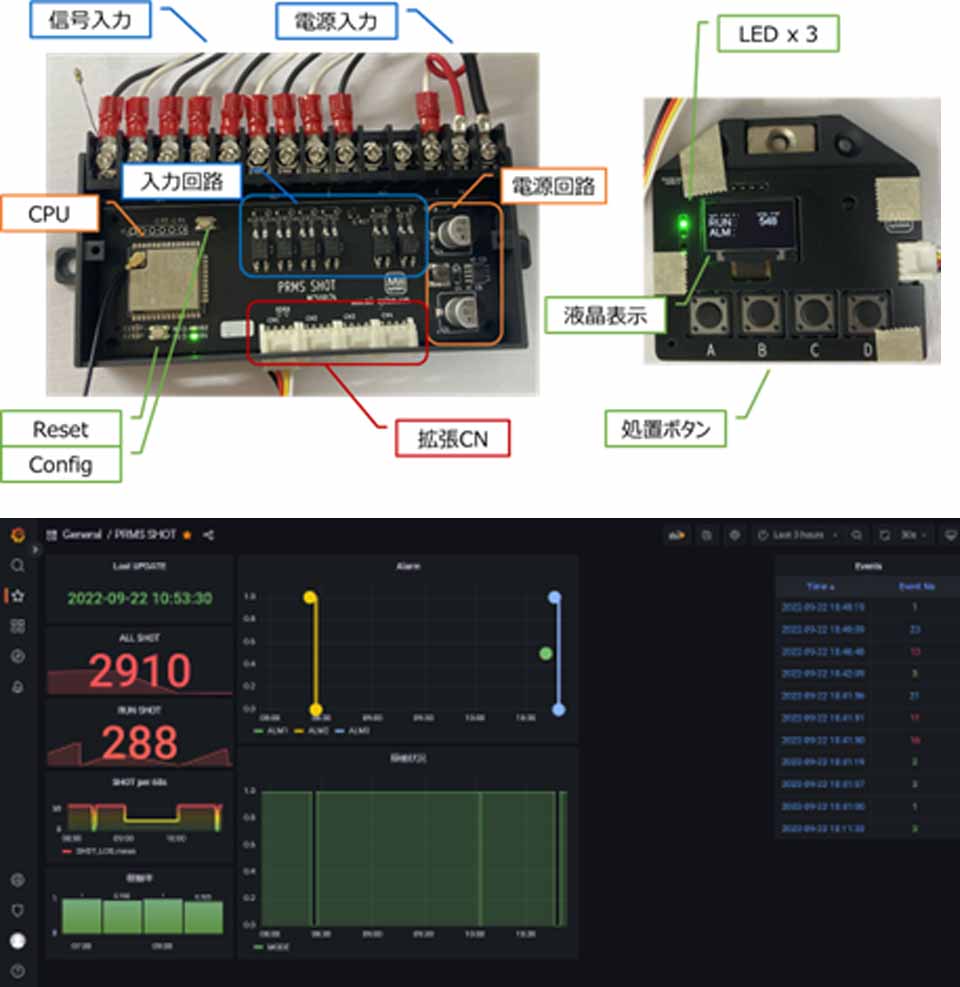
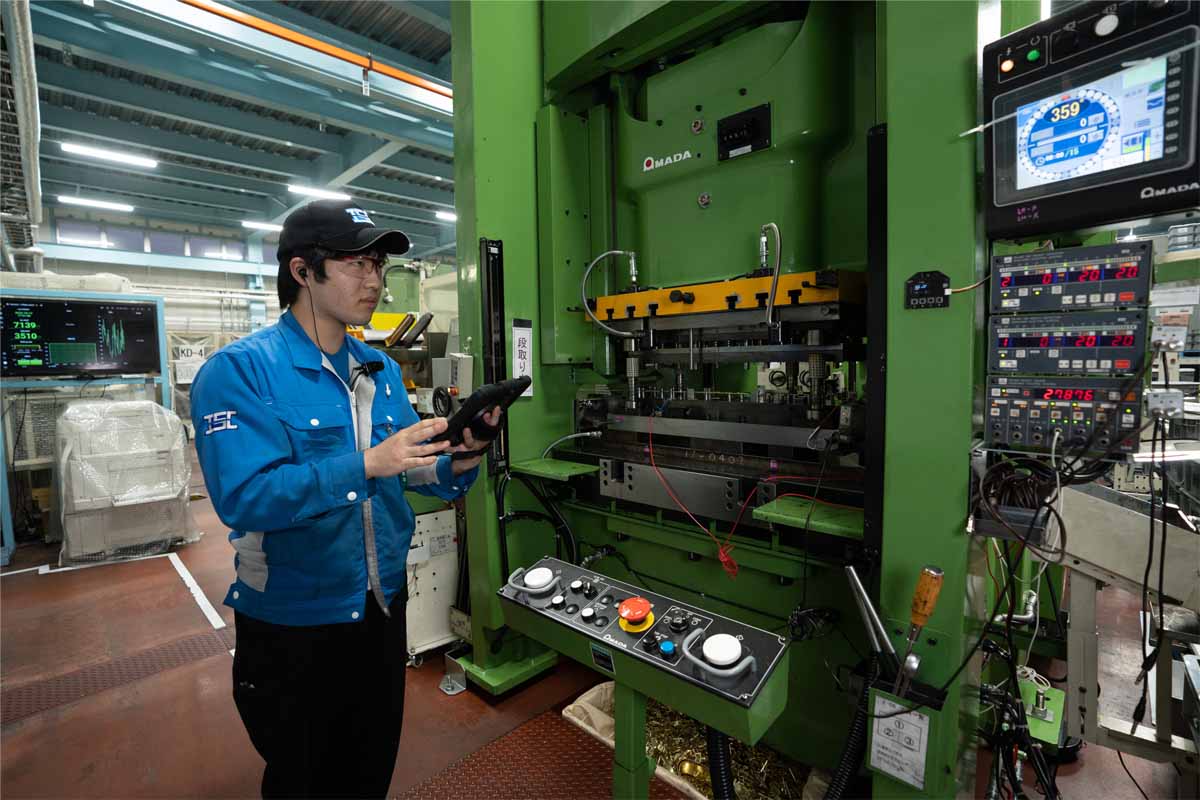
PRMS OIL (Press Remote Monitoring System)
独自開発したセンサとラズベリーパイを利用したプレス潤滑油の流量管理システム。
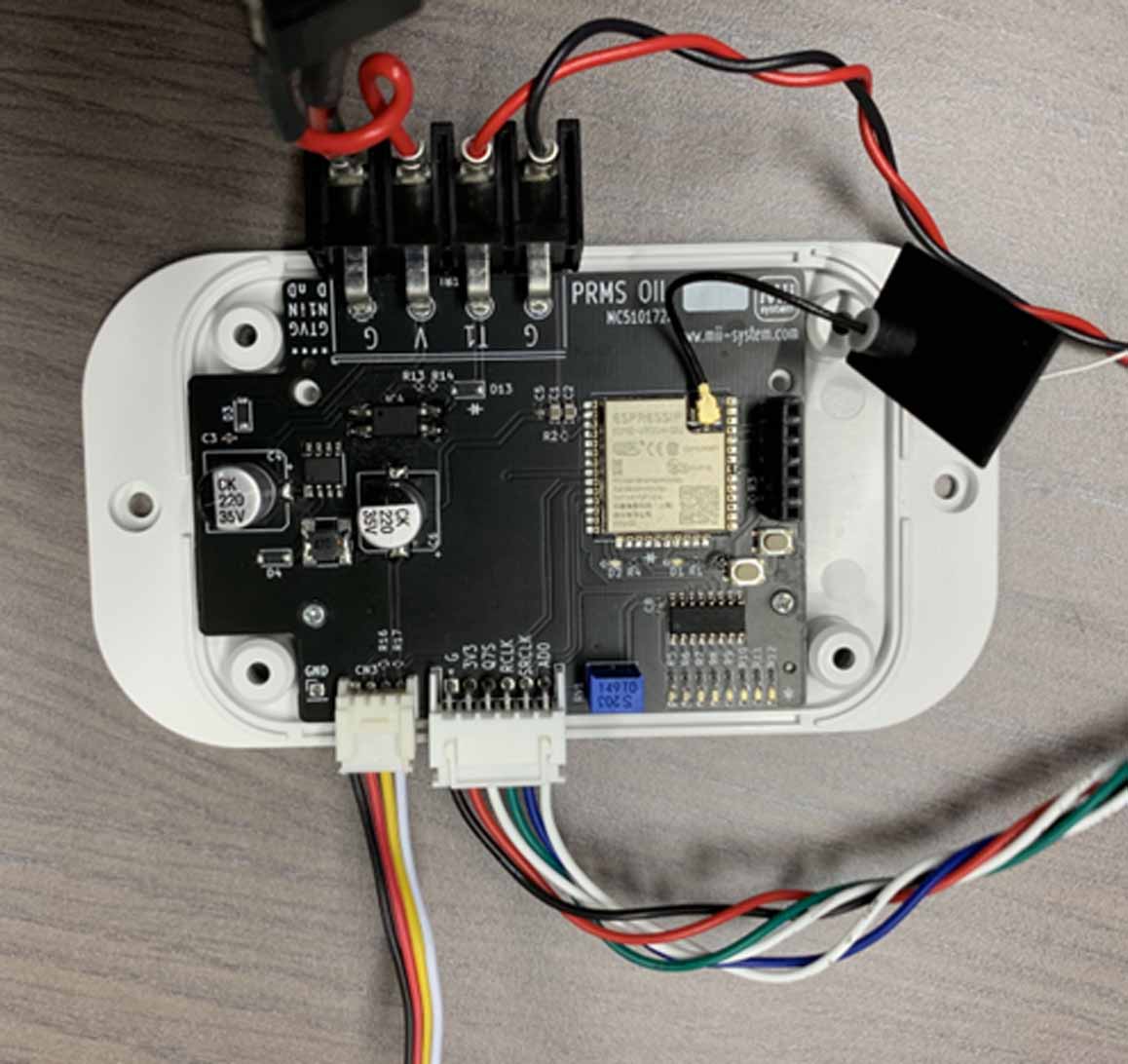
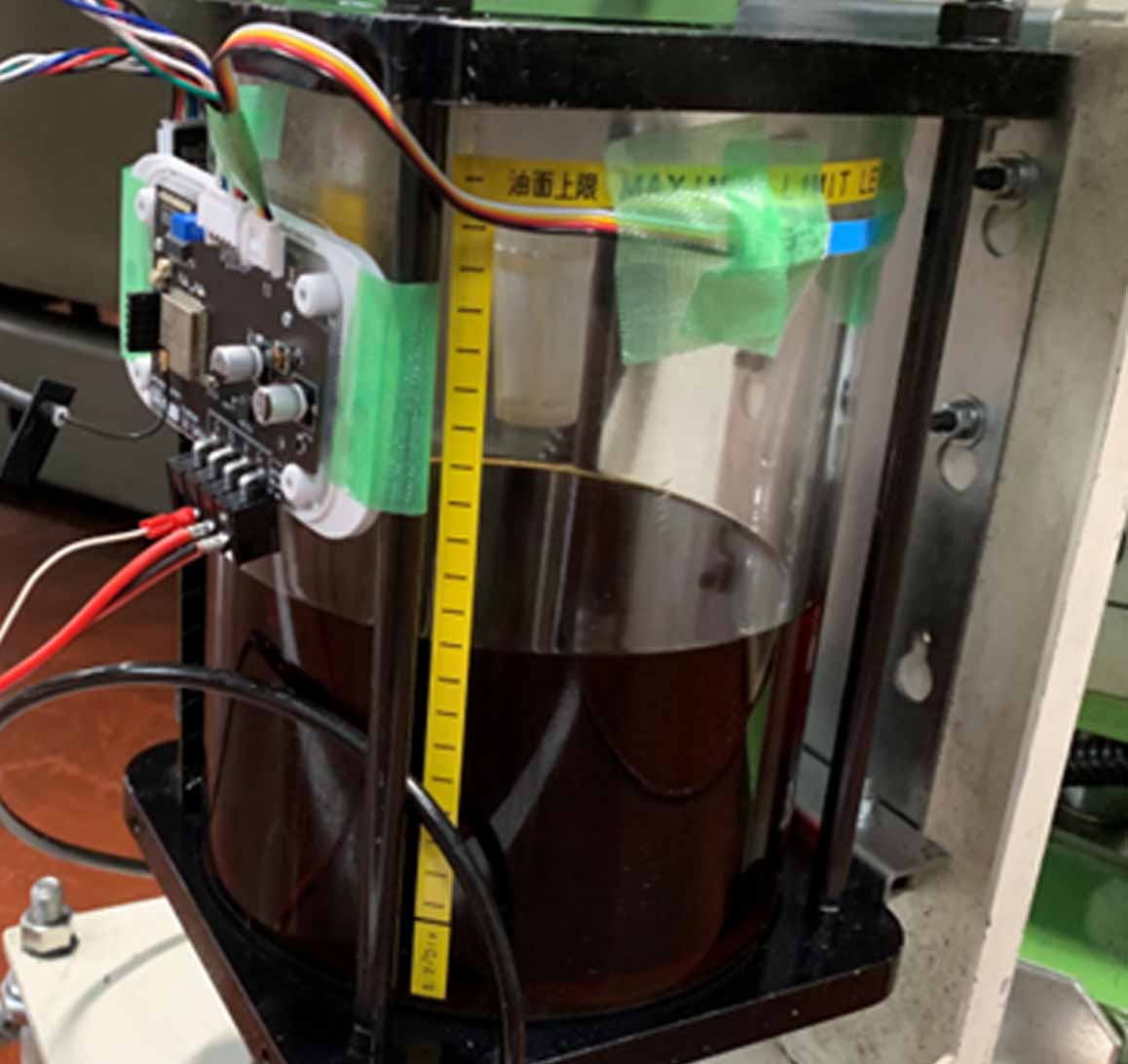
※現在試作開発中です。